Welcome to Vista 3D Technology Co., Ltd.!
Mobile
Application cases
From:惟景三维 Author:Vision3D
222023.09
High-Temperature Online Automated Inspection System for High-Speed Train Wheels
High-speed train wheels are globally acknowledged as technologically advanced products with high production complexity. The manufacturing process involves several steps, including sawing, forging, heat treatment, and machining. The complex forming process poses significant challenges to the stability of the entire automated equipment line. How can we improve product qualification rates while achieving precise control over processing allowances?
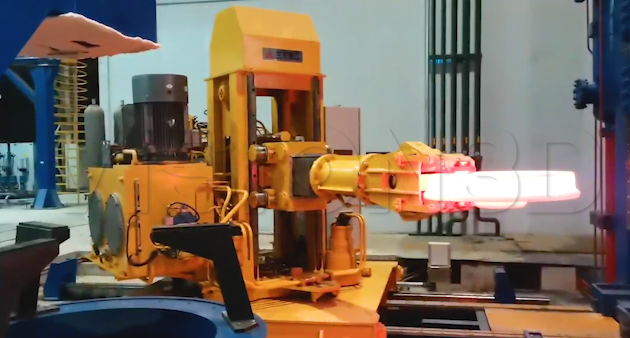
The high-temperature online automated inspection system for high-speed train wheels developed by Vision 3D, is specifically designed to perform automated 3D inspections of train wheels in their red-hot state after the forging process. This system efficiently determines whether the components meet the subsequent processing requirements. It also enables real-time adjustments to the production line's forming parameters based on various measurement data, reducing scrap rates and minimizing material waste.
01 High-Temperature Online Automated Inspection
The temperature of wheel parts is approximately 900℃. No manual intervention is required, and the entire process of loading, unloading, and inspection is automated, with a testing cycle of 30 seconds per piece.
02 Dedicated Precision Analysis Softwar
The software interface consists of a wheel inspection and CAD numerical model comparison interface, a wheel2D cross-section data interface, and a wheel 2D cross-section dimension data interface. 3D images correspond to 2D images. Any cross-section can be selected in the 3D image, and various size information can be displayed in the2D image. up to 500 frames of high-precision cross-sectional data can be stored for each wheel. The data files are small and can be viewed offline on any computer using the software.
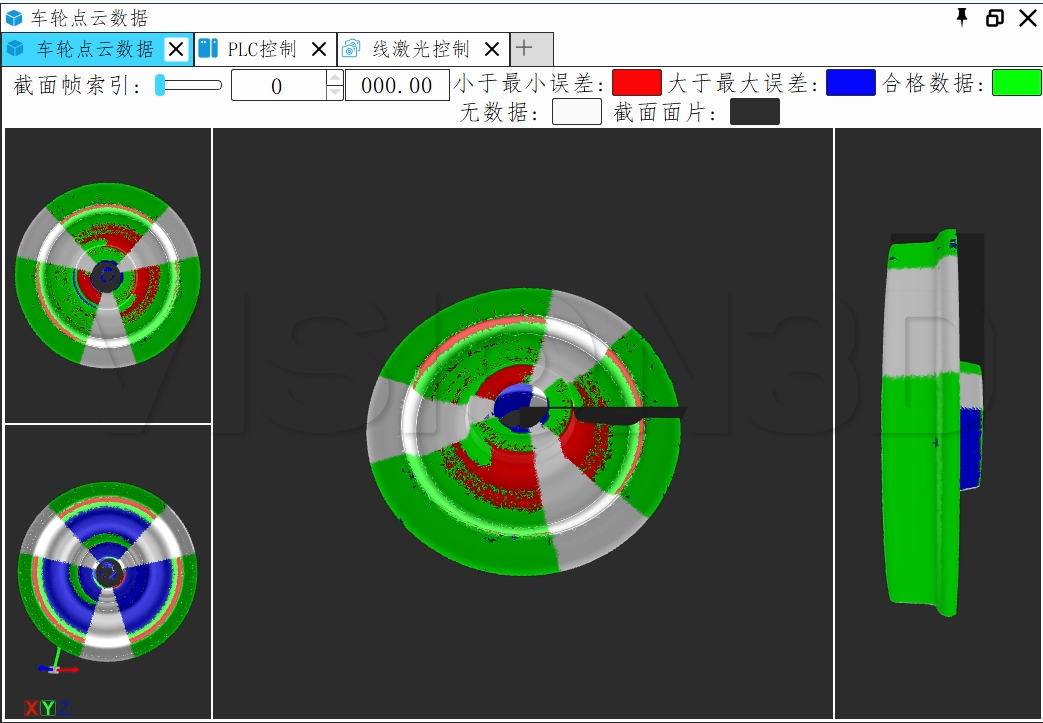
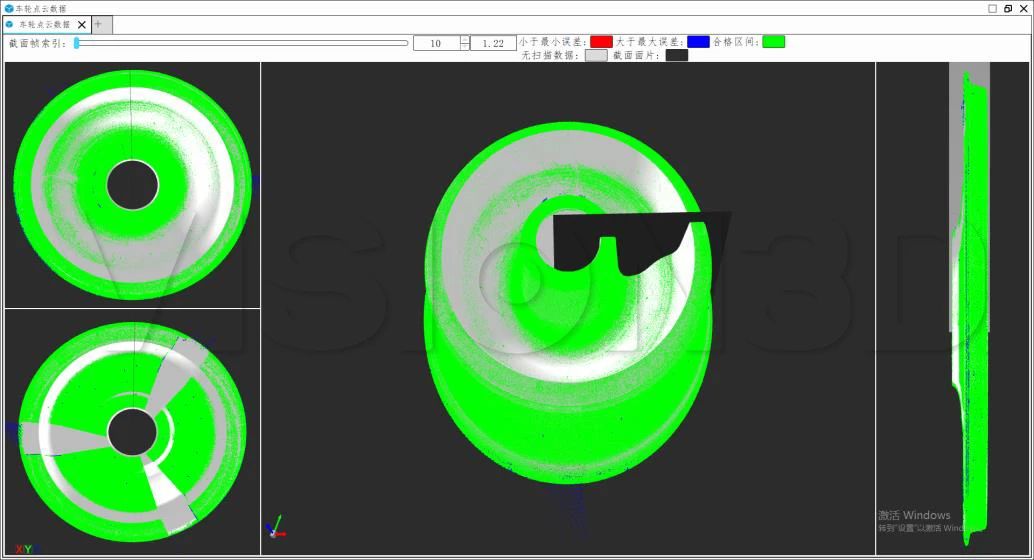
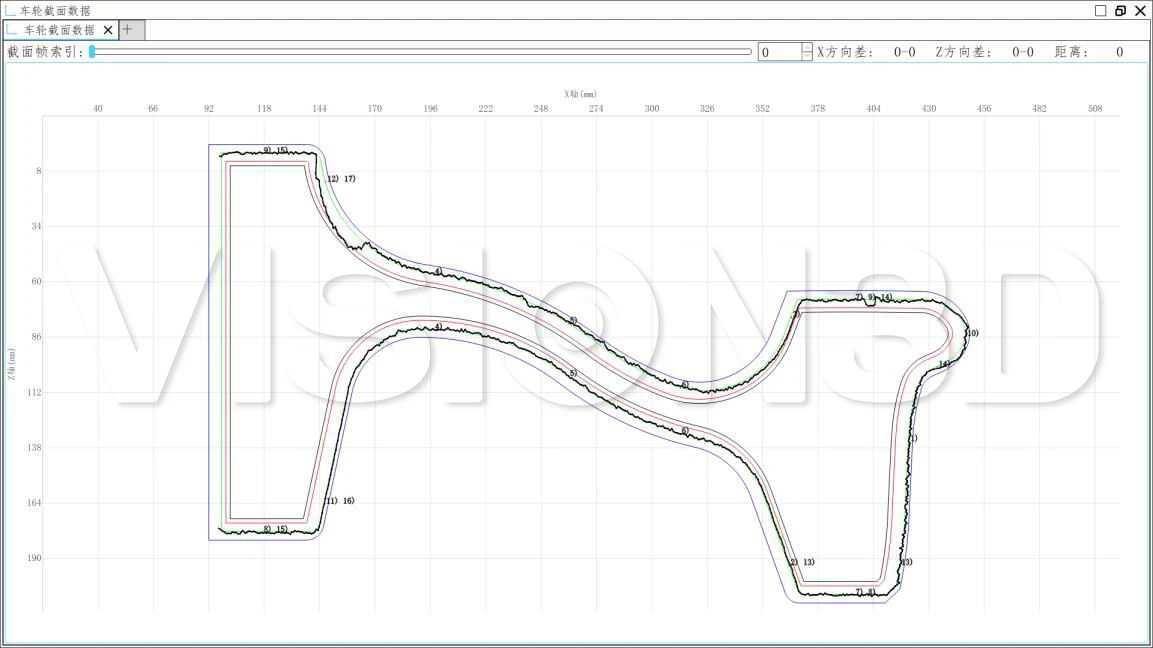
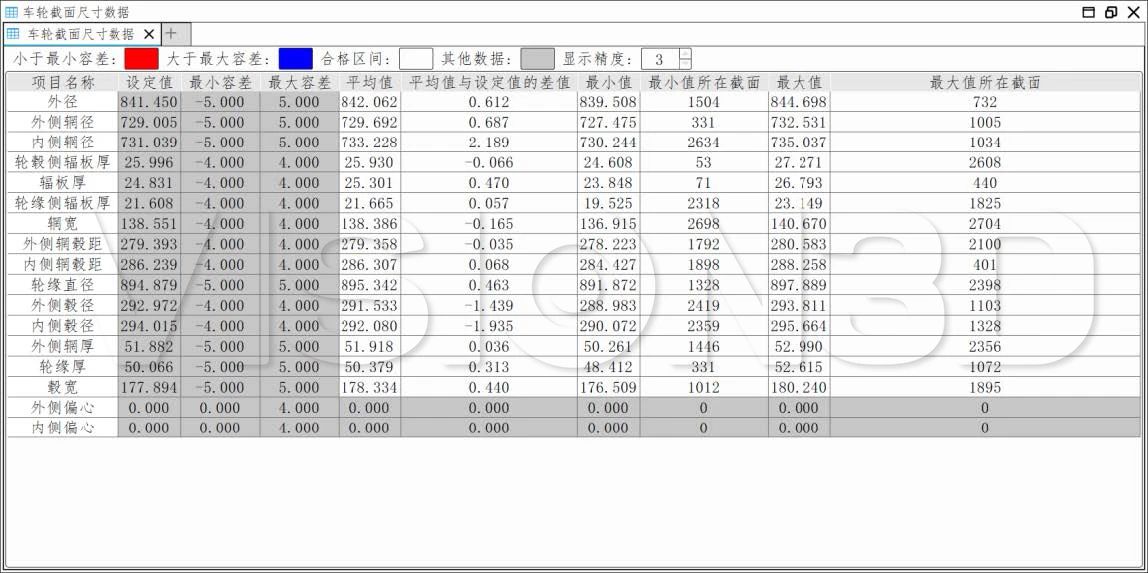
03 Process Optimization Based on Massive Data
The scanned 3D data and inspection reports are automatically stored, allowing users to search for the historical records of the required inspected wheels based on wheel number and creation time. The dimensional accuracy of the parts in the batch production process is statistically analyzed to provide data support for optimizing the forging process in subsequent stages.
Last:
Next:Application cases
-
Pre-sales:sales@vision3d.cnAfter-sales:aftersales@vision3d.cn
-
Pre-sales: 189 7166 9261After-sales:189 7166 8135
-
Consultation